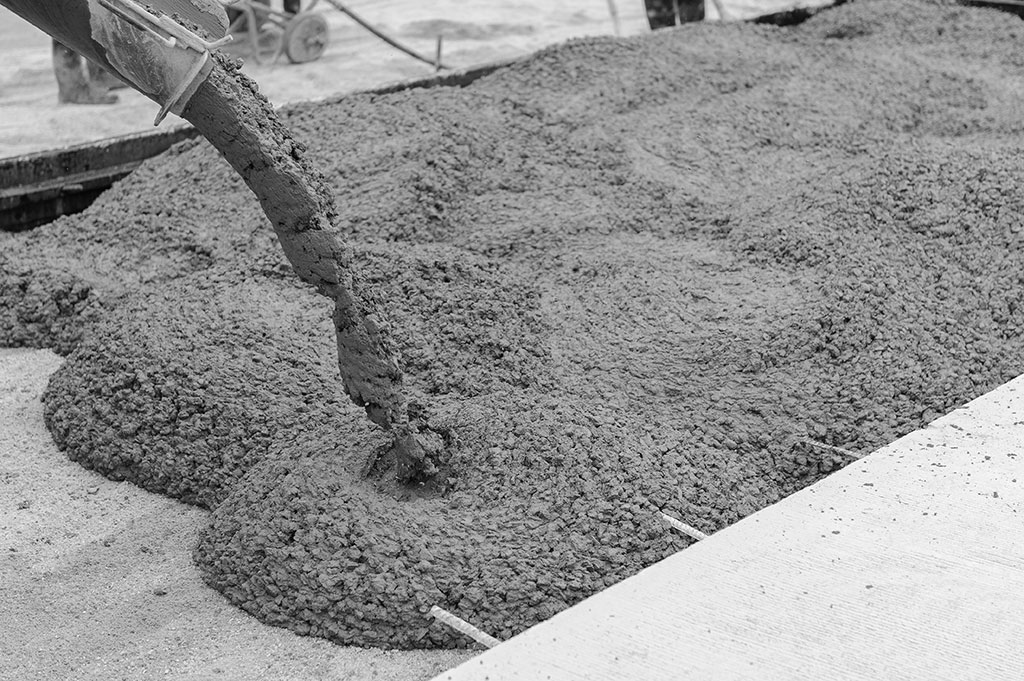
What is it?
Learn how the natural ingredients of concrete combine to form a remarkably strong, durable and economical building material that has been benefiting mankind for millennia.
Concrete Basics
In its simplest form, concrete is a mixture of paste and aggregates (sand & rock). The paste, composed of cement and water, coats the surface of the fine (sand) and coarse aggregates (rocks) and binds them together into a rock-like mass known as concrete.
Within this process lies the key to a remarkable trait of concrete: it’s plastic and can be molded or formed into any shape when newly mixed, strong and durable when hardened. These qualities explain why one material, concrete, can build skyscrapers, bridges, sidewalks, and superhighways, houses and dams.
The key to achieving a strong, durable concrete rests on the careful proportioning and mixing of the ingredients. A concrete mixture that does not have enough paste to fill all the voids between the aggregates will be difficult to place and will produce rough, honeycombed surfaces and porous concrete. A mixture with an excess of cement paste will be easy to place and will produce a smooth surface; however, the resulting concrete will be more likely to crack and be uneconomical.
A properly proportioned concrete mixture will possess the desired workability for the fresh concrete and the required durability and strength for the hardened concrete. Typically, a mixture is by volume about 10 to 15 percent cement, 60 to 75 percent aggregates and 15 to 20 percent water. Entrained air bubbles in many concrete mixtures may also take up another 5 to 8 percent.
Portland cement’s chemistry comes to life in the presence of water. Cement and water form a paste that surrounds and binds each particle of sand and stone. Through a chemical reaction of cement and water called hydration, the paste hardens and gains strength.
The character of concrete is determined by the quality of the paste. The strength of the paste, in turn, depends on the ratio of water to cement. The water-cement ratio is the weight of the mixing water divided by the weight of the cement. High-quality concrete is produced by lowering the water-cement ratio as much as possible without sacrificing the workability of fresh concrete. Generally, using less water produces a higher quality concrete provided the concrete is properly placed, consolidated and cured.
Besides portland cement, concrete may contain other cementitious materials including fly ash, a waste byproduct from coal burning electric power plants; ground slag, a byproduct of iron and steel manufacturing; and silica fume, a waste byproduct from the manufacture of silicon or ferro-silicon metal. Some of these cementitious materials are similar to the volcanic ashes the Romans mixed with lime to obtain their cement binder. Some of these structures still exist today! The concrete industry uses these materials, which would normally have to be disposed in land-fill sites, to the advantage of concrete. The materials participate in the hydration reaction and significantly improve the strength, permeability and durability of concrete.
Other Ingredients
Aggregates for concrete are chosen carefully. Aggregates comprise 60 to 75 percent of the total volume of concrete. The type and size of the aggregate mixture depends on the thickness and purpose of the final concrete product. Relatively thin buildings sections can require small coarse aggregates, though aggregates up to six inches (150 mm) in diameter have been used in large dams. A continuous gradation of particle sizes is desirable for efficient use of the paste. In addition, aggregates should be clean and free from any matter that might affect the quality of the concrete.
Almost any natural water that is drinkable and has no pronounced taste or odor may be used as mixing water for concrete. However, some waters that are not fit for drinking may be suitable for concrete.
Excessive impurities in mixing water not only may affect time and concrete strength, but also may cause efflorescence, staining, corrosion of reinforcement, volume instability and reduced durability.
Specifications usually set limits on chlorides, sulfates, alkalis, and solids in mixing water unless tests indicate that the water will not negatively impact concrete properties.
How Is It Made?
Hydration Begins
After the aggregates, water, and the cement are combined, the mixture remains in a fluid condition for about four to six hours which permits transporting, placing and finishing in its final location, then the mixture starts to harden. All portland cements are hydraulic cements that set and harden through a chemical reaction with water. During this reaction, called hydration, crystals radiate outwards from cement grains and mesh with other adjacent crystals or adheres to adjacent aggregates. The building up process results in progressive stiffening, hardening, and strength development. Once the concrete is thoroughly mixed and workable it should be placed in forms before the mixture becomes to stiff. During placement, the concrete is consolidated to compact it within the forms and to eliminate potential flaws, such as honeycomb and air voids.
Proportioning
The proportioning of a concrete mix design should result in an economical and practical combination of materials to produce concrete with the properties desired for its intended use, such as workability, strength, durability and appearance.
The ready mixed concrete producer may independently select the material proportions to provide the performance you need or may receive instructions through the job specifications, such as minimum cement content, air content, slump, maximum size of aggregate, strength, and others. The RMC producer is the expert in selecting the proportions based on previously developed guidelines and experience.
Regardless of the source of instructions, there are established methods for selecting the proportions for concrete for each batch. The Standard Practice for Selecting Proportions for Normal, Heavyweight, and Mass Concrete (ACI 211.1-91) published by the American Concrete Institute Committee 211 is often referenced for selecting concrete proportions.
Here are the basics of a good concrete mix:
- Cement and water combine chemically to bind the sand and aggregate together. Fly ash or other cementitious materials, which enhance concrete properties may supplement some of the cement. The key to quality concrete is to use the least amount of water that can result in a mixture that can be easily placed, consolidated and finished.
- Fine and coarse aggregates make up about 70% of the concrete volume and impart volume stability to the concrete. Concrete aggregates are required to meet appropriate specifications and in general should be clean, strong and durable.
- Admixtures, are generally products used in relatively small quantities to improve the properties of fresh and hardened concrete. They are used to modify the rate of setting and strength development of concrete, especially during hot and cold weather. The most common is an air-entraining agent that develops millions of tiny air bubbles in concrete, which imparts durability to concrete in freezing and thawing exposure. Water reducing admixtures enable concrete to be placed at the required consistency while minimizing the water used in the mixture, thereby increasing strength and improving durability. A variety of fibers are incorporated in concrete to control cracking or improve abrasion and impact resistance.
How is it Produced?
A. Transit Mixed (or “truck-mixed”) Concrete
In transit-mixed concrete, also called truck mixed or dry-batched, all of the raw ingredients are charged directly in the truck mixer. Most or all water is usually batched at the plant. The mixer drum is turned at charging (fast) speed during the loading of the materials. There are three options for truck mixed concrete:
- Concrete mixed at the job site. While travelling to the job site the drum is turned at agitating speed (slow speed). After arriving at the job site, the concrete is completely mixed. The drum is then turned for 70 to 100 revolutions, or about five minutes, at mixing speed.
- Concrete mixed in the yard. The drum is turned at high speed or 12-15 rpm for 50 revolutions. This allows a quick check of the batch. The concrete is then agitated slowly while driving to the job site.
- Concrete mixed in transit. The drum is turned at medium speed or about 8 rpm for 70 revolutions while driving to the job site. The drum is then slowed to agitating speed.
B. Shrink Mixed Concrete
Concrete that is partially mixed in a plant mixer and then discharged into the drum of the truck mixer for completion of the mixing is called shrink mixed concrete. Central mixing plants that include a stationary, plant-mounted mixer are often actually used to shrink mix, or partially mix the concrete. The amount of mixing that is needed in the truck mixer varies in these applications and should be determined via mixer uniformity tests. Generally, about thirty turns in the truck drum, or about two minutes at mixing speed, is sufficient to completely mix shrink-mixed concrete.
C. Central Mixed Concrete Central-mixing concrete batch plants include a stationary, plant-mounted mixer that mixes the concrete before it is discharged into a truck mixer. Central-mix plants are sometimes referred to as wet batch or pre-mix plants. The truck mixer is used primarily as an agitating haul unit at a central mix operation. Dump trucks or other non-agitating units are sometimes be used for low slump and mass concrete pours supplied by central mix plants. About 20% of the concrete plants in the US use a central mixer. Principal advantages include:
- Faster production capability than a transit-mix plant
- Improved concrete quality control and consistency and
- Reduced wear on the truck mixer drums.
There are several types of plant mixers, including:
- Tilt drum mixer
- Horizontal shaft paddle mixer
- Dual shaft paddle mixer
- Pan mixer
- Slurry mixer
The tilting drum mixer is the most common American central mixing unit. Many central-mix drums can accommodate up to 12 yd3 and can mix in excess of 200 yd3 per hour. They are fast and efficient, but can be maintenance-intensive since they include several moving parts that are subjected to a heavy load.
Horizontal shaft mixers have a stationary shell and rotating central shaft with blades or paddles. They have either one or two mixing shafts that impart significantly higher horsepower in mixing than the typical drum mixer. The intensity of the mixing action is somewhat greater than that of the tilt drum mixer. This high energy is reported to produce higher strength concrete via to thoroughly blending the ingredients and more uniformly coating the aggregate particles with cement paste. Because of the horsepower required to mix and the short mixing cycle required to complete mixing, many of these mixers are 4 or 5 yd3 units and two batches may be needed to load a standard truck or agitator.
Pan mixers are generally lower capacity mixers at about 4 to 5 yd3 and are used at precast concrete plants.
Slurry Mixing
The slurry mixer is a relative newcomer to concrete mixing technology. It can be added onto a dry-batch plant and works by mixing cement and water that is then loaded as slurry into a truck mixer along with the aggregates. It is reported to benefit from high-energy mixing. Another advantage is that the slurry mixer reduces the amount of cement dust that escapes into the air.
“Mix Mobiles” – Mobile Volumetric Proportioning Plants
“Mix Mobile” are truck-mounted, volumetric batching and continuous mixing units. These “plants-on-wheels” often supply small-volume or specialty pours and offer the convenience of freshly mixed concrete in fairly precise quantities. The unit consists of a truck with bins of sand, coarse aggregate, cement, water, and admixtures. The aggregate bins have longitudinal belts at the bottom of the sand, and as well as coarse aggregate bins that drag the aggregate to separate adjustable gates at the rear of the bin. The speed of the belts is connected to a feeder in a cement bin, and all three materials drop down into a mixer. Flow meters control the introduction of water and admixtures.
Plant Styles, etc.
Concrete batch plants come in a variety of styles and configurations designed to accommodate a variety of markets, technical and environmental considerations.
- Portable Plants In general, they have a cement silo and an overhead bin for sand or one or two coarse aggregates.
- Permanent Plants The plant operates from same location for a relatively long period of time. Large quantities of materials of greater variety are stored at the plant. The plant will tend to have larger overhead storage and may have two lanes to permit batching two trucks at the same time. Plants may be also classified as
- High profile – The traditional stack up plant is a tall plant that has aggregate and cement storage bins that feed into batchers or weigh hoppers by gravity.
- Low profile – The aggregate weigh hoppers are near the ground with belts to elevate the aggregate to load the mixer.
Delivery of Ready Mixed Concrete
The Truck Mixer
While ready mixed concrete can be delivered to the point of placement in a variety of ways, the overwhelming majority of it is brought to the construction site in truck-mounted, rotating drum mixers. Truck mixers have a revolving drum with the axis inclined to the horizontal. Inside the shell of the mixer drum are a pair of blades or fins that wrap in a helical (spiral) configuration from the head to the opening of the drum. This configuration enables the concrete to mix when the drum spins in one direction and causes it to discharge when the direction is reversed.
To load, or charge, raw materials from a transit mix plant or centrally mixed concrete into the truck, the drum must be turned very fast in the charging direction. After the concrete is loaded and mixed, it is normally hauled to the job site with the drum turning at a speed of less than 2 rpm.
Since its inception in the mid-1920’s, the traditional truck-mixer has discharged concrete at the rear of the truck. Front discharge units, however, are rapidly becoming more popular with contractors. The driver of the front discharge truck can drive directly onto the site and can mechanically control the positioning of the discharge chute without the help of contractor personnel. Currently, because of weight laws, the typical truck mixer is a 9 to 11 yd3 unit. The drums are designed with a rated maximum capacity of 63% of the gross drum volume as a mixer and 80% of the drum volume as an agitator. Generally, ready mixed concrete producers, load their trucks with a quantity at or near the rated mixer capacity. Fresh concrete is a perishable product that may undergo slump loss depending on temperature, time to the delivery point on the job site, and other factors.
Water should not to be added to the mix unless the slump is less than that which is specified. If water is added, it should be added all at once and the drum of the truck mixer should be turned minimum of 30 revolutions, or about two minutes, at mixing speed.
The ASTM C 94, Specification for Ready Mixed Concrete, indicates that the concrete shall be discharged on the job site within 90 minutes and before 300 revolutions after water was added to the cement. The purchaser may waive this requirement, when conditions permit.
In certain situations, air-entraining, water reducing, set-retarding or high-range water reducing admixtures may need to be added to concrete prior to discharge to compensate for loss of air, high temperatures or long delivery times. The ready mixed concrete producer will assist the purchaser in such circumstances.
Inspection and Testing of Ready Mixed Concrete
Concrete is a manufactured product. Specific control tests and evaluations are required during the manufacturing process to produce predictable high-quality concrete. The customer may want to verify that concrete meets specifications. Some of the important properties of concrete that are measured by basic quality control tests are strength, temperature, slump, air content, and unit weight. In general concrete is tested at a frequency of 1 in 150 cubic yards.
Each test helps to determine the quality of concrete and it should be performed in accordance with American Society for Testing and Materials (ASTM) standards. A certified ACI Concrete Field Testing Technician – Grade I, must make the tests.
When there are no formal job specifications, such as with a homeowner or small contractor, it is important for the concrete producer to agree to furnish concrete in accordance with ASTM C 94 or at least certain critical sections of ASTM C 94. This reference should also be included on the delivery ticket.
ASTM C 94 includes a number of things that should be a part of any agreement between the producer and a purchaser. Some of them are:
- Define the basis of purchase, cubic yards, and how it is measured.
- Define acceptable material specifications and acceptable industry practice and tolerances.
- Define strength testing procedures and acceptance criteria.
- Set laboratory personnel qualifications. The testing laboratory must comply with ASTM C 1077, which is required in ASTM C 94.
Types of Concrete
Precast
Precast concrete is concrete cast elsewhere than its final position. Precast construction can be used to produce a wide variety of structural elements such as wall panels, bridge girders, pipes, poles, crash barriers, lift stations, etc. The concrete can be reinforced, lightly prestressed or prestressed depending upon its requirements. Precast concrete elements are typically transported from the plant to the job site through highways, rail, or barges. Tilt-up concrete is a form of precast concrete and is generally referred to as site precasting.
Tilt-Up
Tilt-Up construction is “a construction technique of casting concrete elements in a horizontal position at the jobsite and then tilting and lifting the panels to their final position in a structure”. The greatest advantage of tilt-up construction over cast-in-place concrete is the ease and speed of construction. Generally the concrete should attain a high early age flexural strength to facilitate lifting and handling. Tilt-up concrete is a form of precast concrete and is generally referred to as site precasting.
Flowable Fill
Flowable also known as constrolled low-strength material (CLSM) is a self-compacted, cementitious material used primarily as a backfill in lieu of compacted fill. The compressive strengths must be lower than 1200 psi and often is lower than 200 psi. Since the material flows into place no compaction is required which is a significant advantage over compacted back fill. Flowable fill can be made with very high amounts of non-standard materials.
Pervious Concrete
Pervious concrete is concrete that does not contain fine aggregate. It typically has a voids content of 15% to 35%. This ensures that the concrete has the unique ability to allow storm water to pass through its mass into the ground underneath. Pervious concrete offers significant environmental benefits as it reduces the requirement for drainage facilities. Further it facilitates the recharge of ground water and the filtration process purifies the water as it percolates below.